Workflow
Ein technologisches Meisterstück
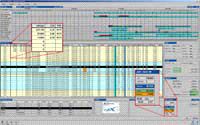
Freitag 31. August 2007 - Erster Anwender Europas, der Druckereibüro, Vorstufe, Drucksaal und Rotation per JDF vernetzt
Die Druckerei Ferdinand Berger & Söhne Ges.m.b.H. in Horn, etwa 50 km nördlich von Wien im Waldviertel ansässig, ist einer der führenden Zeitschriftendrucker Österreichs mit über 200 Titeln. 40% des Umsatzes von zuletzt etwa 57 Mio. Euro macht die Magazinproduktion aus. Broschüren, Kataloge und Werbedrucksachen aller Art generieren weitere 40%, die auf den vier Rotationen und neun Bogenoffsetmaschinen produziert werden. Dazu kommt eine perfekt ausgestattete Weiterverarbeitung mit Sammelhefter, Klebebindestraße und weiterem Equipment, mit dem auch Bücher und Kleindrucksachen (auch im Digitaldruck) verarbeitet werden. Die etwa 250 Mitarbeiter bewältigen etwa 7.500 Aufträge pro Jahr für Kunden, die aus dem Inland (80%) und Ausland (20%) kommen. Jährlich werden dabei etwa 30.000 Tonnen Papier bedruckt.
Das Unternehmen wurde 1868 von Ferdinand Berger gegründet und ist nun in der 4. und 5. Generation in Familienbesitz. Ab 1986 nahm die Druckerei einen rasanten Aufschwung, als man mit einer gebrauchten Harris M200 in den Rollenoffsetdruck einstieg und diesen kontinuierlich durch laufende Neuinvestitionen ausbaute. Als 1998 der Maschinenpark aus einer Heidelberger M600 und einer Harris M300 bestand, wurde dieser um eine 24-Seiten Sunday-Press 1998 erweitert und im Jahre 2002 die Harris M300 gegen eine Heidelberg M600 getauscht. Zwischenzeitlich stieg Berger in den Digitaldruck ein, ist heute einer der größten Digitaldrucker Österreichs, und reduzierte gleichzeitig sein Engagement im Endlosdruck. 2006 startete Berger die größten Bauaktivitäten in der Unternehmensgeschichte, als für eine MAN Roland Lithoman IV eine 5.500 qm große Halle gebaut wurde, die seit März 2007 in Betrieb ist. Mit der 48-Seiten-Rotation soll die starke Position des Unternehmens im Zeitschriftenmarkt weiter ausgebaut werden. Gleichzeitig wurde die Vorstufe mit neuester CtP-Technologie ausgestattet, mit einer Kolbus Publica 12.000 die modernste Klebebindestraße in Österreich installiert und der Betrieb via JDF und Hiflex MIS vernetzt.
Hiflex MIS ist Dreh- und Angelpunkt
Was in der Aufzählung logisch oder nahe liegend klingt, ist jedoch das Resultat konsequenter Optimierungsprozesse im Unternehmen. Vor allem die jetzt realisierte Vernetzung der wesentlichen Unternehmensbereiche ist um es mit dem gebührenden Respekt auszudrücken ein technologisches Meisterstück. Das seit Ende 2000 installierte Hiflex MIS ist zum Dreh- und Angelpunkt der Produktion geworden und mit Vorstufe, Drucksaal und Rotation vernetzt. Damit ist die Druckerei Berger das erste Unternehmen in Europa, das eine Rollenoffsetmaschine über die Hiflex-Dispo per JDF ansteuert.
Dabei hat alles mit einer kleinen Broschüre angefangen. Initialzündung für die Idee der Vernetzung war ein Folder zum Thema JDF, den ich auf der drupa 2004 mitgenommen habe, schildert Michael Schwayda, Leiter Produktionssteuerung bei Berger. Daraus entwickelte sich zunächst das Verfeinern der Kalkulationsdaten im Hinblick auf eine spätere Vernetzung via JDF. Was der Sachbearbeiter ohnehin schon machte, wurde nun mit allen Konsequenzen im Hinblick auf den Rollenoffset optimiert. So werden bereits bei der Anlage eines Auftrags Parameter wie Rollenbreite, Falzart, Strangführung, Falzart in der Rotation, Beschnitt, Leimung etc. berücksichtigt. Und der Einsatz des einen oder anderen Papiers erfordert unterschiedliche Parameter bei der Rasterweite, der Farbe, den Profilen und den Farbdichtewerten. All dies muss in der Auftragsbearbeitung bereits berücksichtigt und erfasst werden. Wobei sich die Hiflex Software und die im Hintergrund arbeitenden Datenbanken und deren Verknüpfungen erleichternd auswirken, so Michael Schwayda. Aber das alles galt es ja in der Projektphase zu berücksichtigen und in den Workflow einzubeziehen. Und er gesteht ein, dass alle am Prozess Beteiligten ordentlich dazu gelernt haben. Denn erst bei der Projektarbeit und der Definition des Workflows wurde die Vielzahl der einzelnen Arbeitsschritte und Parameter deutlich.
Arbeitsfluss: Hiflex an Vorstufe
Nach Auswahl der letzten Ausgabe eines Periodika-Auftrags und dem Blick in dessen Kalkulation erzeugt der Sachbearbeiter durch Kopieren, Änderung der Ausgabe, Auflage und Lieferdatum einen neuen Auftrag. Dabei kann der Produktaufbau (beispielsweise eine Änderung der Seitenzahl) modifiziert und für den neuen Auftrag die entsprechend zugeordnete Kalkulation aktualisiert werden. Gleichzeitig ermittelt Hiflex MIS den neuen Produktionsweg durch die Auto-Pilot-Funktion. Damit stehen je nach Auftrag die optimalen Druck- und Verarbeitungsparameter und Produktionsmittel fest. So wurde beispielsweise festgelegt, dass der Inhalt auf der Rotation läuft, während der Umschlag im Bogenoffset gedruckt wird.
Im Auftrag werden vom Sachbearbeiter auch die Ecktermine für Datenübergabe, Imprimatur, Farbabstimmung etc. eingetragen. Sobald der Auftrag abgespeichert ist, erhält der Sachbearbeiter die Information, dass eine JDF-Datei erzeugt wurde, die an die Vorstufe übermittelt wird und der Auftrag auch der Disposition zur Verfügung steht. Der vom Sachbearbeiter an die Vorstufe übertragene JDF-File (der neben Auftragsnummer, Auftragsname und Kunde auch die Aufteilung der Produktteile beinhaltet) löst die automatische Anlage des Auftrages in :ApogeeX aus. Aufgrund der Kalkulationsdaten des Hiflex MIS wird in :ApogeeX ein entsprechender Baum erstellt, in dem neben den geplanten Druckmaschinen auch die Rasterweite (entsprechend der Farbigkeit, Druckverfahren und Papierqualität) vorgegeben ist. Nach den Prepress-Prozessen wie Preflight, Paginierung, Trapping etc. spalten sich die Prozesse aufgrund der in der Auftragskalkulation definierten unterschiedlichen Druckmaschinen. Es wird auf entsprechend hinterlegte Ausschießschemata zugegriffen, die PDFs werden zugeordnet und in den Ausschießer geladen. Auf Basis der in der Kalkulation angelegten Daten wie Farbigkeit, Papierart, Rasterweite etc. werden nunmehr die entsprechenden Profile der Druckmaschinen geladen und die Daten zur Belichtung an die Lüscher-CtP-Systeme gesendet. Während die Rollenoffsetmaschine via JDF die Produktionsdaten erhält, werden für den Bogenoffset die Farbvoreinstelldaten aus der Vorstufe übertragen.
Disposition an Rotation und zurück
Jeder Auftrag steht nach Auftragsanlage sofort der Disposition zur Verfügung. Dort werden auf Basis der Eckdaten des Sachbearbeiters die Planungsdetails wie Drucktermin und Priorität ergänzt. In der Plantafel der Disposition werden die Aufträge dann in der geplanten Reihenfolge in einem Zeitstrahl angezeigt. Sobald die Disposition von der Vorstufe die Information erhält, dass die Platten bereitstehen (Anzeige in einem Statusfenster), können die JDF-Daten mit den Produktionsdaten an die Druckmaschine gesendet werden. Im PECOM-System der 15 m/s schnellen Lithoman verschmelzen die Produktionsdaten aus dem Hiflex MIS und die Farbdaten aus der Vorstufe zu einem Job pro Druckbogen. Sämtliche druckrelevanten Daten einschließlich einer Vorschau des druckenden Sujets sind nun im PECOM-System vorhanden: zum Beispiel Nutzen und Auflage, Farbwerksbelegung, Papierqualität, Grammatur und Bahnbreite. Wird eine schmalere Bahn für den Auftrag benötigt, werden die äußeren Farbzonen in Abhängigkeit von der Bahnbreite automatisch geschlossen. Auch der Farbtyp wird entsprechend der eingesetzten Papierqualität automatisch ausgewählt. Über die im Hiflex Auto-Pilot errechneten Produktionsdaten erfolgt eine Zuordnung zu den hinterlegten Muster-Falzschemata am Maschinenleitstand der Rotation, so dass der Falzapparat automatisch eingestellt wird. Mit Hilfe der JDF-Voreinstelldaten wird die Rotation bei Folgeformen in nur 15 Minuten wieder auf Produktion gebracht. Bei einem Komplettwechsel (andere Druckbreite, andere Farben etc.) liegt die Rüstzeit bei 45 bis 60 Minuten. Während der Produktion wird der Disposition zusätzlich zu den BDE-Rückmeldungen (Betriebsdatenerfassung) aus dem Hiflex MIS auch per JMF-Message (Job Messaging Format) der augenblickliche Maschinenzustand mit Auftragsnummer, Bogennummer, Druckgeschwindigkeit, Anzahl gute Exemplare und Anzahl Maku in Echtzeit angezeigt.
Ein Riesenschritt vorwärts
Bis März 2007 wurde das Hiflex MIS nur für die üblichen Funktionen wie Kalkulation, Materialwirtschaft etc. eingesetzt. Doch parallel zur Planung für die Produktion mit den neuen Maschinen wurde auch das Vernetzungsprojekt vorangetrieben. Start für die Lithoman war der 12. März 2007. Bis dahin musste die Anbindung fertig sein. Wobei wir wussten, dass wir mit einer Lernphase rechnen mussten. Natürlich gab es anfangs Jobs, die nicht zu hundert Prozent in Ordnung waren und die manuell korrigiert werden mussten. Doch das haben wir längst im Griff, schildert Michael Schwayda. Und was sich seit der Realisierung der Vernetzung verändert hat? Der einzelne Sachbearbeiter trägt jetzt mehr Verantwortung, erläutert Michael Schwayda. Dabei müssen Sachbearbeitung und Vorstufe höchst präzise arbeiten. Aber mit etwas mehr Aufwand im Vorfeld der eigentlichen Produktion lassen sich Fehler vermeiden, Prozesse optimieren und Zeit einsparen.
Das Projekt wird bei der Druckerei Berger noch weiter vorangetrieben. Schließlich gibt es Bereiche des Unternehmens, die noch nicht in den Workflow eingebunden sind. Dabei wird jedoch genau analysiert, wo eine weitere Vernetzung aus wirtschaftlicher Sicht Sinn macht und wo nicht. Schließlich hat man bei Berger nun einige Erfahrung in Sachen vernetzte Druckerei. Und Michael Schwayda weiß: Es gibt keine fertige Vernetzungs-Lösung die kann kein Hersteller anbieten. Aber zusammen mit Hiflex und den anderen an der Vernetzung beteiligten Unternehmen haben wir es geschafft, das Projekt umzusetzen. Wenn wir heute einen Job aufrufen sind alle notwendigen Daten da! Genau das ist es, was den gesamten Herstellungsprozess optimiert. Und schmunzelnd fügt er hinzu: Die Vernetzung unterstützt uns dabei, unsere Zeitschriftenproduktion im Kleinauflagenbereich auch auf der Rotation kostengünstig zu produzieren.
PS: Das Institut für rationale Unternehmensführung (IRD) zeichnete die Druckerei Berger im Mai dieses Jahres mit dem IRD-Zertifikat „Best-Practice in der Druckindustrie“ mit Spitzenleistung im Schwerpunkt „Bereichsübergreifende Automatisierung“ aus.