Drucksaal
Basis zur Druckfarbenproduktion 4.0
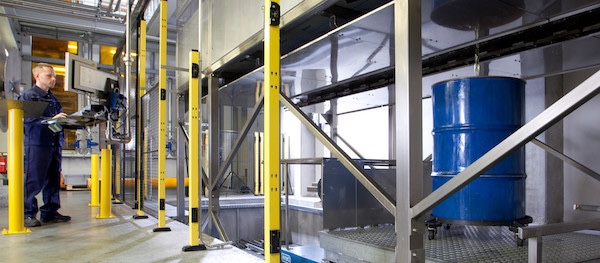
Mittwoch 01. März 2017 - Durch automatisierte Dosierung erzielt Zeller+Gmelin eine präzisere Farbrezeptierung und schont gleichzeitig Ressourcen
Der verantwortungsbewusste Umgang mit Rohstoffen ist für Unternehmen aus ökologischer und wirtschaftlicher Sicht gleichermaßen ein wichtiger Grundsatz. In der Abschlusserklärung des G7-Gipfels in Elmau vom Juni 2015 wurden konkrete Anstrengungen gefordert, um mit der globalen Allianz für Ressourceneffizienz reale Ergebnisse zu erzielen. Das Land Baden-Württemberg hatte bereits im November 2013 eine Initiative „100 Betriebe für Ressourceneffizienz“ ins Leben gerufen. Dafür hatte sich auch der Druckfarbenhersteller Zeller+Gmelin GmbH & Co. KG beworben. Im Fokus standen Maßnahmen, die entweder Einsparungen oder eine verbesserte Nutzung von Ressourcen in der Produktion ermöglichen. Das Eislinger Unternehmen war mit seiner Bewerbung erfolgreich, die auf der Einführung einer computergestützten Rohstoffdosierung basierte. Die Vorteile wie das Vermeiden von Dosierfehlern und die Reduzierung von Dosierverlusten sind im vorliegenden Artikel ebenso beschrieben wie die Ergebnisse des Projektes.
Der Bereich Druckfarben des Unternehmens Zeller+Gmelin ist auf die Herstellung von UV-härtenden Farben und Lacken für das Marktsegment des Verpackungs- und Etikettendrucks spezialisiert. In den letzten Jahren ist speziell in der Lebensmittelindustrie eine kontinuierlich steigende Sensibilisierung der Konsumenten und Verbraucherorganisationen hinsichtlich möglicher Migrationsrisiken zu beobachten. Es wird befürchtet, dass Bestandteile von Druckfarben durch das Verpackungsmaterial in Lebensmittel übergehen könnten.
Wachsende Ansprüche von Verbrauchern und Gesetzgeber
Deshalb sind bei der Rezeptierung von Druckfarben, die für Lebensmittelverpackungen eingesetzt werden, besonders hohe Anforderungen zu erfüllen. Darüber hinaus ist aufgrund neuer gesetzlicher Vorgaben immer häufiger eine Anpassung von Farbrezepturen erforderlich. Diese stetige Herausforderung, die Formulierung der Farben und Lacke mit den Anforderungen abgleichen zu müssen, bedingt gleichzeitig den Optimierungsbedarf beim Herstellungsprozess.
Die moderne Farbenproduktion unterliegt der Verpflichtung zur Guten Herstellungspraxis gemäß europäischer GMP-Verordnung (Good Manufacturing Practice). Demnach hat der Druckfarbenhersteller ein Qualitätssicherungssystem für sämtliche Produktionsabläufe festzulegen und anzuwenden. Speziell bei der Einwaage von Rohstoffen, bei der das Risiko von Rohstoffverwechslungen und Kontaminationen besteht, dient es dazu, möglicherweise weitreichende Auswirkungen bis zum Endverbraucher zu vermeiden. Das Qualitätssicherungssystem bietet weiterhin die Möglichkeit, durch die verbesserte Beherrschung der Produktionsprozesse die Ressourceneffizienz zu steigern.
Industrie 4.0 als Zukunftsaufgabe im Blick
Aus diesem Grund hat Zeller+Gmelin die Zielsetzung verfolgt, alle Dosierungen von Flüssigrohstoffen nicht mehr durch manuelle Verwiegung, sondern über ein computergestütztes, vollautomatisches Dosiersystem vorzunehmen, das direkt an das hausinterne ERP-System angebunden ist. Auf diese Weise wird auch die Basis für Industrie 4.0 bei Zeller+Gmelin gelegt.
Die Realisierung des Vorhabens wird in erster Linie durch die sehr hohe Viskosität der UV-Bindemittel erschwert. Gleichzeitig sind diese Rohstoffe sehr temperatur- und scherempfindlich, so dass sich eine automatische Dosierung aus Vorratstanks extrem schwierig gestaltet. Eine weitere Herausforderung ist das grammgenaue Dosieren dieser zähflüssigen Komponenten.
Gesamtkonzept als Lösungsansatz
Um diese anspruchsvolle Aufgabe erfüllen zu können, wurde ein neues Rohstofflager mit entsprechend temperierten Vorratstanks konzipiert. Das Lager wurde mit direktem Anschluss zur Dosieranlage geplant, so dass die Transportwege der flüssigen Dosierkomponenten so kurz wie möglich sind. Weiterhin galt es, Pumpen zu finden, die besonders scherarm und energieeffizient arbeiten, um bei relativ hohen Dosiermengen die Bindemittel trotzdem schonend zu fördern
In enger Abstimmung mit Pumpen- und Dosieranlagenherstellern wurden über einen längeren Zeitraum an einer Einzel-Pilotdosieranlage verschiedene Pumpensysteme und Dosierventilsysteme erprobt. Nach einer über einjährigen Testphase wurde zusammen mit der Firma Füll Systembau GmbH ein Lager- und Dosieranlagenkonzept entwickelt und mit den entsprechend schonenden und erfolgreich getesteten Pumpensystemen geplant. Zur tatsächlichen Realisierung des Konzeptes war am Ende noch zusätzlich der Bau einer neuen Lager- und Fertigungshalle notwendig, die um das Dosiersystem herum geplant und erstellt wurde. In diesem neuen Gebäude wurden zwei Tanklagereinheiten installiert und speziell für die hochviskosen Produkte ein Wärmelager in unmittelbarem Anschluss an die Dosiereinheit angebracht. Dieses Wärmelager wird über eine Wärmepumpe beheizt, welche im Kühlwasserkreislauf installiert ist und die Prozessabwärme der bisherigen Fertigung nutzt.
Fehlerfreie Einwaage hilft Ressourcen sparen
Die vollautomatische Dosierung eliminiert im Hinblick auf Genauigkeit, Korrektheit und Schnelligkeit den Fehlerfaktor Mensch und stellt die vollumfängliche Reproduzierbarkeit sicher. Seit der Einführung ist die Fehlerquote bezogen auf Falscheinwaagen auf Null gesunken. In der Folge hat sich der Ressourceneinsatz spürbar reduziert.
Das neue System hat zudem die Entleerung der Gebinde mit hochviskosen Harzsystemen optimiert. Dadurch konnte die bis dahin erforderliche Fassbelieferung auf größere IBC-Gebinde (Intermediate Bulk Container) umgestellt werden, was zugleich den Transportaufwand reduziert und zu einer effektiveren Lagernutzung führt. In der Produktion ist zudem eine einfachere Handhabung mit verbesserten ergonomischen Arbeitsprozessen zu verzeichnen. Als zusätzlicher Nebeneffekt hat sich auch der Gebindeabfall reduziert.
Ein wichtiger Vorteil ist vor allem auch die Restentleerung der Container, die sich durch eine genaue Abstimmung mit dem Dosierkonzept deutlich verbessert hat. Die Produktanhaftung konnte von teilweise 3 bis 5% auf unter 1% gesenkt werden, so dass durch die fast vollständige Restentleerung nur noch geringe Mengen zu entsorgender Reststoffe anfallen und kaum noch Arbeitsmittel gereinigt werden müssen. Dementsprechend sinkt auch die Menge des durch Reinigungsprozesse belasteten Abwassers auf ein Minimum.
Rationalisierung entschärft Kostendruck
Insgesamt wurden die Produktionsprozesse erheblich rationalisiert, so dass Spielräume entstanden sind, dem steigenden Kostendruck entgegenzuwirken. Nach der Umstellung von manueller auf vollautomatische Verwiegung, die eine optimale Reproduzierbarkeit gewährleistet, ist die Prozessabteilung Einwiegerei nicht länger der Engpass im Produktionsablauf und Quelle von Fehlchargen, die aufwändig entsorgt werden müssen. Der Durchsatz hat sich deutlich erhöht, obwohl gleichzeitig von einem 3-Schichtbetrieb auf einen zweischichtigen Betrieb umgestellt werden konnte
Die Einführung des neuen Systems hatte vielfältige Einsparungen zur Folge. So wurde der Rohstoffschwund um ca. 8 bis 10 t pro Jahr reduziert, was Rohstoffeinsparungen in Höhe von ca. 40 000 bis 60 000 Euro entspricht. Weiterhin konnte durch den Wegfall der Nachtschicht in den Bereichen Strom, Druckluft, Gas etc. etwa ein Drittel der Energie eingespart werden. Durch kompaktere Gebindeeinheiten konnten Rohstoffbelieferungen reduziert werden, so dass die CO2-Emissionen der Wareneingangslogistik um 20% gesunken sind. Schließlich ist anzumerken, dass inzwischen die anfallende Abwärme der Produktionsanlagen über eine Wärmepumpe im Kühlwasserkreislauf zur Raumluftbeheizung und als Prozesswärme in der Dosieranlage genutzt wird.
Fazit
Die Umsetzung des Projekts hat zum einen gezeigt, wo Ressourcen eingespart werden können. Gleichzeitig hat es zusätzliches Verbesserungspotenzial für die Arbeitsplatzgestaltung eröffnet, z.B. durch eine wesentliche Reduzierung der Hebe- und Tragetätigkeiten. Rationalisierungseffekte auf verschiedenen Ebenen sorgen inzwischen für eine Verbesserung der Wettbewerbsfähigkeit. Eine weitere Folge des automatischen Dosierkonzeptes ist die Steigerung der Prozesssicherheit und die Einhaltung der GMP-Anforderungen. Bis 2016 war ein Umsetzungsgrad von 60% erreicht. Für zukünftige Projekte und Anforderungen ist das Konzept modular erweiterbar.
Initiative präsentiert Praxisbeispiele effizienter Ressourcennutzung
Das Projekt „100 Betriebe für Ressourceneffizienz“ wurde 2013 von der Allianz für mehr Ressourceneffizienz zwischen den führenden Wirtschaftsverbänden des Landes Baden-Württemberg und der Landesregierung initiiert. Die Initiative zeigt anhand von 100 ausgewählten Exzellenzbeispielen, wie Ressourceneffizienz konkret umgesetzt werden kann und welcher Nutzen damit verbunden ist. Die bisherigen Aktivitäten zur Ressourceneffizienz werden so mit konkreten, vorzeigbaren Ergebnissen unterstützt. Damit sollen weitere Unternehmen zum Mitmachen gewonnen werden.
Durchgeführt wurde das Projekt gemeinsam vom Institut für Industrial Ecology (INEC) an der Hochschule Pforzheim, der Landesagentur Umwelttechnik BW und dem Institut für Arbeitswissenschaften und Technologiemanagement (IAT) der Universität Stuttgart.
Zur Allianz für mehr Ressourceneffizienz gehören das Ministerium für Umwelt, Klima und Energiewirtschaft Baden-Württemberg, das die Arbeiten dieses Forschungsprojektes auch mit Mitteln des Ministeriums gefördert hat, der Landesverband der Baden-Württembergischen Industrie e.V. (LVI), der Baden-Württembergische Industrie- und Handelskammertag e.V. (BWIHK), der Verband der Chemischen Industrie e.V. (VCI), Landesverband Baden-Württemberg, der Verband Deutscher Maschinen und Anlagenbauer Baden-Württemberg (VDMA) und der Zentralverband Elektrotechnik und Elektroindustrie (ZVEI), Landesstelle Baden-Württemberg.